CASE 眼科用治療機器
構想設計
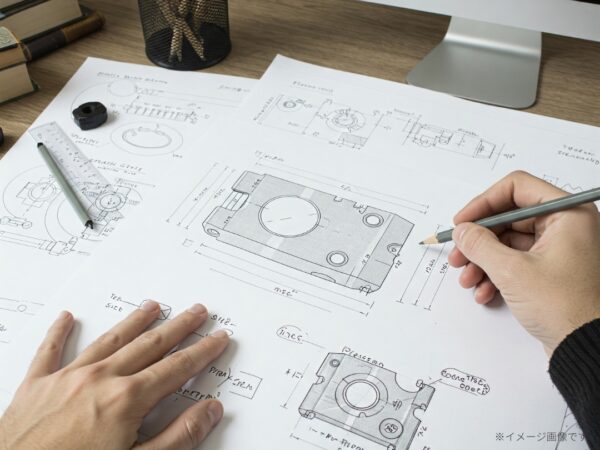
医療系の展示会(メドテック)に出展していた当社ブースにて、お客様より現状の生産体制に不安を抱いておられる点のご相談をいただき、お取引及びすり合わせをスタートするに至りました。
眼科機器の販売をされているお客様は、現状で生産は協力企業様にて多くの工程を依頼されておりましたが、ご依頼先の企業様の高齢化や情報取り纏めの煩雑さに効率化ができない現状に悩まれておりました。当社では一貫して生産可能な体制が整っているため、生産の移管に関し検討を進めていくと、図面と実際の部品に差異が多くあることが分かり、製造・組立工程の属人化からその差異が生まれている現状が見えてまいりました。
特に機器の組立工程では、ご担当されている職人さんによる微修正が多く発生しており、手順書もないため他の人工や企業に引き継ぐことができないことも判明いたしました。
既に生産をしている既製品ではありますが、図面や工程の統一を行うべく、当社に再設計のご依頼をいただき、製造移管に向けたプロジェクトを進めていくこととなりました。
要素検討/試験
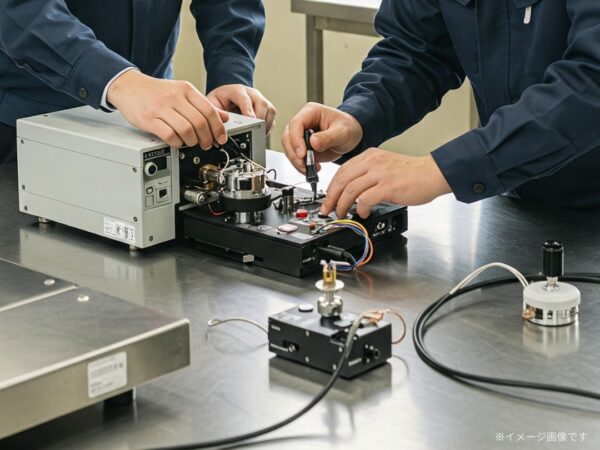
本件では第一に、全図面の見直しによる属人化の排除と、それに伴う現物合わせによる組立作業の簡易化を目標としております。
現状の不明瞭な部分を精緻化するため、お客様より機器をご提供いただき、すべての部品を測定→3Dモデルを作成いたしました。これにより根幹部分等ユニット・部品単位でのすり合わせを進め、再設計の方向性を固めていく方針となりました。3Dを作成して部品を図面と照らし合わせた結果、お客様も把握されていなかった差異が多く発見されることとなり、その一つ一つに関してどのように改善していくのか、またはどのように改善し機能向上していくのか、時間をかけて機器の全体を検討していくことになります。重要なのは、ただ図面化するのではなく、改善・機能向上につなげるための設計思想と実現可能性のバランスをすり合わせ、部品の材質や熱・表面処理の有無、または鋳型による製造+機械加工など、ありとあらゆる製造方法からコストや品質等保守性・再現性を加味した選定を行っていくことです。この工程で機器の全体像や機能の再検討を完了いたしました。
基本設計
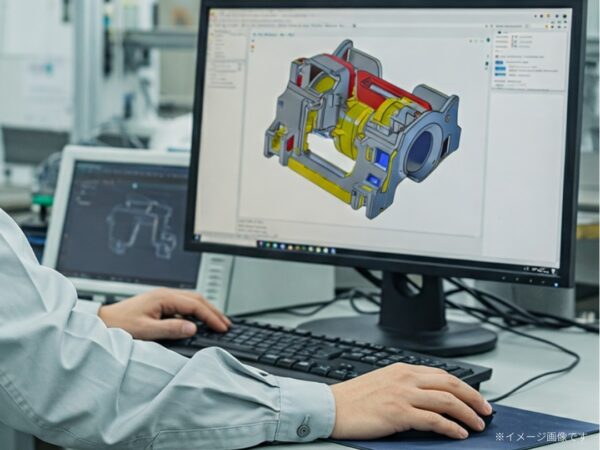
これまでお客様でお困りだった点で、図面と部品の整合性が取れない状況がございました。初期段階の図面はあるものの、様々な変更が加わった部品は図面と全く違う様相を呈していたそうです。前段階で3Dを作成した私たちは、図面化に伴い現物と初期図面との差異の具体化を行い、お客様と内容を都度確認・検討し、どのような構造にするか、また部品レベルでは設定する公差を必要最低限にすべく、他部品との相関を踏まえた検討を進めました。構造の強度や干渉に関しては3Dデータを基に解析を行い、必要最低限の公差を実装することでコストの低減につなげ、全図面の精査を行うことで現物の情報も図面に落とし込み、データ内に全ての情報を揃えることができました。また、設計変更部分はお客様とのすり合わせの中で一部製作を行い、使用感の確認や摺動性等の評価なども行いました。すべてをデータ上で行っても現物でのトラブルは数多く発生します。試作機を作成する前に簡易的に確認できる現物を使用して感覚の目合わせを行ったことも、スムーズな進行の要因となりました。
詳細設計
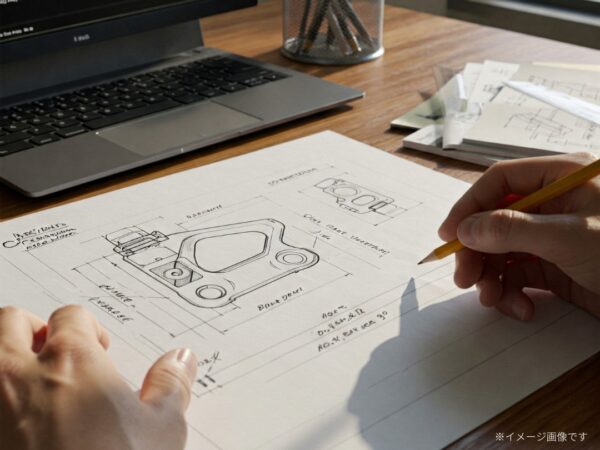
3Dデータ、図面データ、部品リストなど、基本設計までで出揃ったデータを基に試作機の製作に向け最終検討を行いました。
前述した公差内容に関しても改めて内容の再検討を行い、現物合わせとなっていた箇所の構造や組立手順などもどのように統一するべきか、お客様と入念な打ち合わせをさせていただきました。例えばサンプルによる摺動性の評価を行っていた部品は一定の評価はできたものの強度及び安定性に若干の不安要素を見出すに至り、詳細設計の段階で材質・処理内容の修正を行いました。また、試作機を製作した後もお客様とすり合わせを継続しており、より良い装置とするべく設計変更を引き続き行っております。
上記の設計変更に伴い図面のレビジョン管理もしており、以前お困りになられていた図面と製品の差異は完全に除去することができました。製造・組立ノウハウは図面や手順書に全て紐づいているため、図面通り製作することで「個体差の無い」機器が出来上がるようになりました。
当たり前のように聞こえますが、今回のように製作工程の属人化は様々なパターンで実在します。これは必ずしも悪い事ではないのですが、調達のご担当者様にとってお困りの種となってしまうのは避けられません。今回の件でお客様には大変ご好評をいただき、量産に関しても当社にご依頼いただく結果となりました。