投稿日:2021年10月27日
私たちOEM装置設計・製造.comでは、医療機器や食品機械、半導体製造装置などを、材料や購入品の手配から始まり機械加工・組立・電装・調整まで行い、ご指定の納期までに完成品を納入させていただく…といった社内一貫での装置製造を行っております。さらには加工や組立、板金・樹脂・表面処理や熱処理、材質等ありとあらゆる要素を検討し直した上で、VA/VE提案をお客様へご提供させていただいております。
今回のテーマは「リバースエンジニアリング」です。
――――――――――――――――――――――――――――――――――――――――
リバース(逆行)エンジニアリング(工学)のことで、通常の図面などの設計された製作方法に沿って行うものづくりとは逆に、機械や製品(実物)の分解・観察等を通して構造や構成要素を分析し、そこから製造方法や動作原理などを導き出していくことを指します。
――――――――――――――――――――――――――――――――――――――――
このページの運営会社である「ZESTIA(以下“当社“)」がお客様からの依頼を受け、「現物と図面の齟齬の解消・製品価値の向上」を実現したご提案の事例をご紹介します。この事例を通して、お客様の装置の「受注量」が10%も上昇しました!
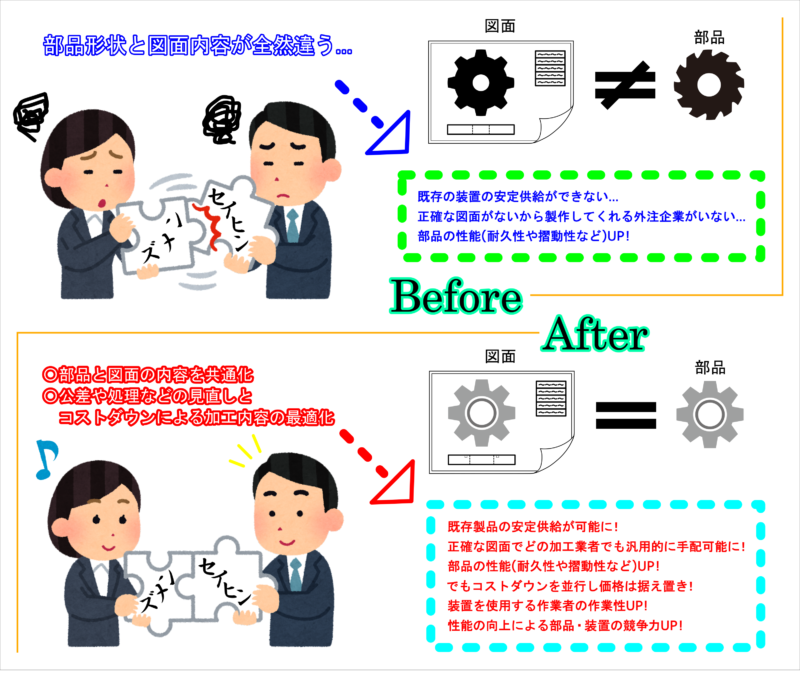
担当者)この部品、よく見たら全然図面指示通りじゃない…!!
当社とお取引のあるA社さん。複数の装置を取り扱っているメーカーであり、担当のBさんは既存の装置の手配を担当していました。リピートの受注という事で繰り返し発注している企業にいつものように製作依頼をしたBさんでしたが、協力企業のC社さんから製作を断られてしまいました。理由としては業務の拡大やそれに伴うキャパオーバー、及び価格対応が難しくなった…等があります。そこでBさんは他の協力企業に依頼を出します。そこで問題が発生しました。
依頼した製品が上がってきていざ組立を始めたところ、なんと装置に部品が適合しませんでした。製作ミスかと協力企業に問い合わせをしますが、確認したところ図面通りの形状・公差になっており、製作が正確に行われておりました。…ですが該当部品に機能上求められる特性が実装できておりません。摺動性及び耐久性、公差部分の差異等に加え、なんと形状すらも、全くの別物になっていたのです。このような図面と実加工品の大きな乖離は、これまで依頼をしていたC社側で切削性や公差の必要性などを判断し、変更が加えられていたようです。その内容はA社側へのフィードバックもなく、変更内容の提示もしてもらえなかったため、再現性が著しく損なわれていました。そのためBさんは装置に必要な部品の調達に困ってしまったのです。
A社様は設計に対して責任を負わなければいけない立場として、勝手な設計変更を無断で行われていたことは看過できず、現在でも協力企業へ依頼される際、設計変更に関しては「心配してしまうポイントの一つ」となっています。
ZESTIAでは部品加工から組立・電装・調整までトータルでサポートできることが強みの一つです。また、その経験やノウハウを活かし、装置の各箇所にどのような機能が求められ、「機能の向上」と「コストの低減」といった相反するテーマを両立させつつ改善するにはどうすれば良いのか…詳細な検討を行い、お客様へご提案させていただく「改善・コストダウン提案(VA/VE)」を行わせていただいております。
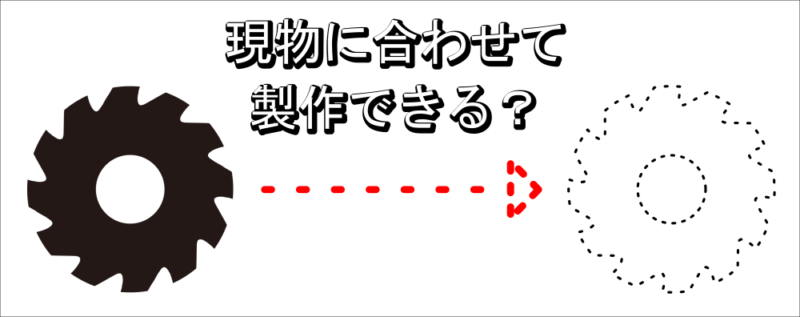
担当者)できるだけ現物に合わせて製作してほしいんだけど…
困っていたBさんは、展示会がきっかけで部品加工のご依頼を頂いていた当社に問い合わせをしてくださいました。まず現状をヒアリングした当社担当者は、客観的で明確な情報の少ない状況を打開するため、既存の部品を1つお借りして材質や構造・製作の意図を解析することから始め、図面に記載されている公差などではやはり該当部品に求められる性能(摺動性や耐久性)が実現できない、との結論に至りました。その上でC社の行った変更内容及びその意図の検討を行った結果、次のような要素が浮かび上がりました。
・材質の変更 : 鋳物 → 鋳物の成分変更(耐久性の向上)
・加工前の鋳物の形状変更 : 切削量の削減
・寸法公差の変更 : 例)h7→±0.15(工数の削減)
変更内容やその意図をBさんともすり合わせ、上記の3点が浮かび上がってきました。現状に合わせ同様の製作を行うことも可能でしたが、今をしのぐだけの対応では当社が加工から撤退した場合、Bさんは同様に困った状況になってしまいます。フィードバックするだけではなく、当社のコストダウンのノウハウを活かして改善提案をさせて頂き、かつ内容を図面に起こす運びとなりました。
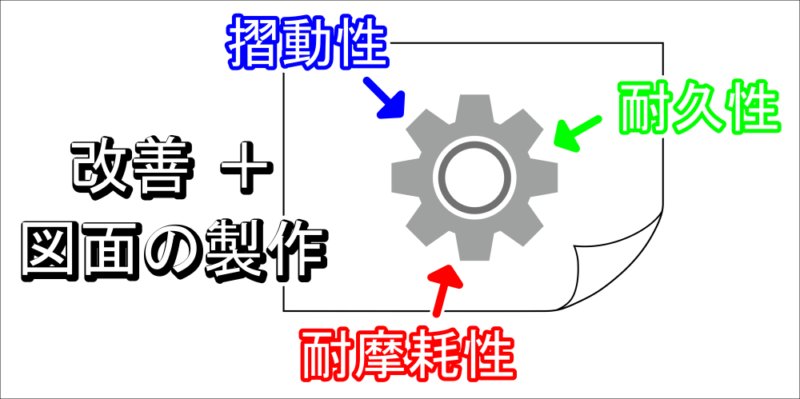
ZESTIA)使用用途に合わせた製品・図面の最適化をしましょう!
当社が提案した改善内容は以下の通りです。
・材質の鋳物の調質内容の見直し : 摺動性の向上
・材料の形状見直し : ブロックからの切削品に変更(鋳型が必要なくなる)
・表面処理の変更 : 塗装 → 硬質アルマイト(耐久性の向上)
上記は新たに提案→採用された内容になり、既存部品の旧図面からの変更点も含めて新しい図面の作成を行いました。新たに処理を加えたり材質の見直しをしたり…など機能向上+単価低減を合わせて行うことで、価格はそのままに機能性の向上を実現することができ、かつ誰が見ても分かるような図面への正確な情報の実装を実現しました。
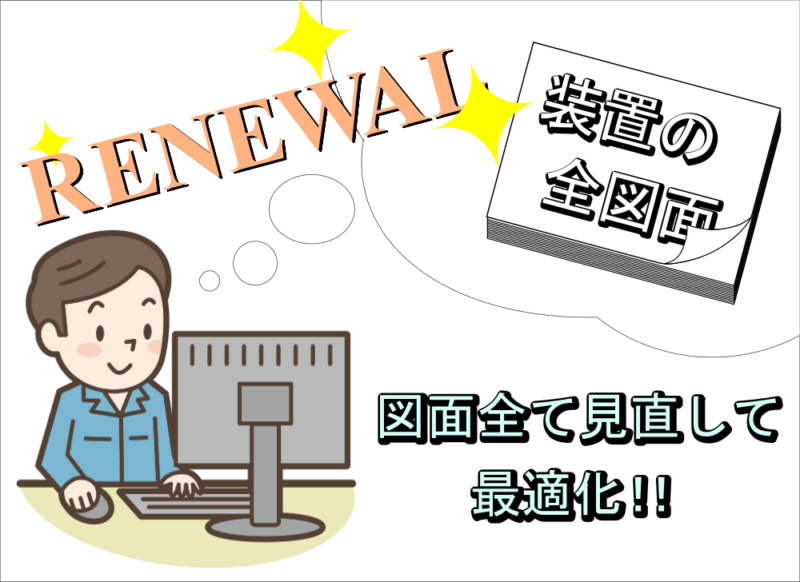
担当者)装置全体の最適化(見直し)はできる? → ZESTIA)もちろんです!!
図面起こしに+αで当社得意のコストダウン・機能向上提案を行ったことでBさんに大変喜ばれ、該当装置の全図面を一度大きく見直すこととなりました。それというのもこのユニットは20年前の設計で、お客様の意見などを取り入れつつ製作が続いていたため、当初なかった「後付けの機構や部品」が原因となり“作業性の低下”など、図面の正確性の低下以外にも黙認されていた問題点が多々あったのです。
ユニット全体の図面を1枚1枚見直し、前述のような図面の一新及び実作業者の作業性を織り込んだ「トータル設計」を行いました。例えば20年前の段階ではラインの中央に設置することで作業者がユニットに「多方向から」アクセスできたのですが、ラインが増えたことで「1方向から」しか操作できなくなった…など、ユニットを取り巻く周辺環境の変化なども含め、現状に最適な設計を行いました。省スペースでも作業者の煩わしさを解消するための提案をさせて頂きました。
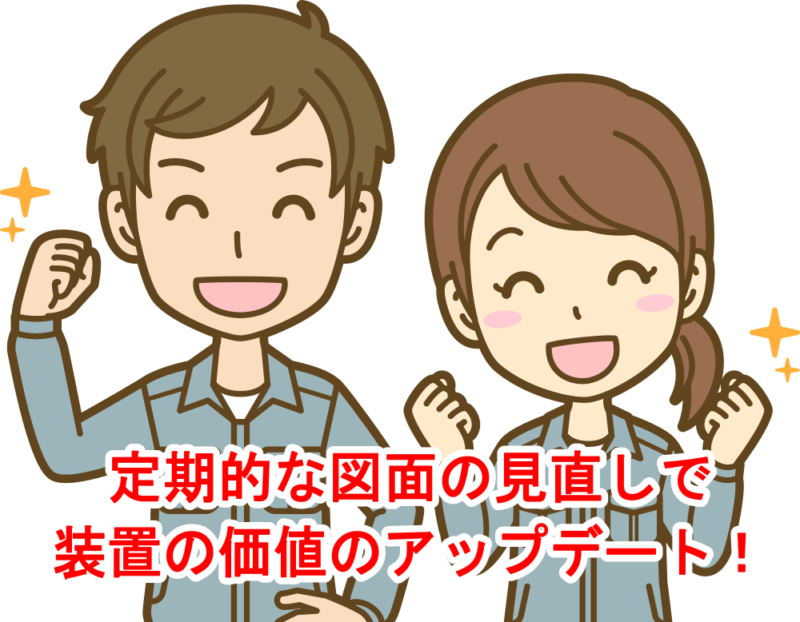
リピート品の定期的な最適化(見直し)の必要性
部品1つにとどまらず、ユニット全体を大きく見直すことになった本案件ですが、構造から大きな変更をしております。ですがここでご紹介する事例としては珍しく、コストダウン自体はあまり大きくございませんでした。…というのもA社さんの希望で機能性の向上(内容・程度はA社とすり合わせ検討)を多く盛り込んだことが一因です。ですが多くの機能向上を盛り込んでも価格は上昇しておりません。機能向上のための工数が増えてもその分他の部品でコストダウンして相殺することができたのです。その結果、該当ユニットはコストはそのままに機能の向上を実現し、結果として競合他社の類似製品に比べて競争力を大きく向上することができました。
その後、この ユニットの受注量が10%も向上 したようです。
機能の向上には手間やコストがかかるものですが、付加する内容の選定やかかるコストを他の部分のコストダウンで相殺するなど、お客様にも、私どものような受注企業にも、双方に都合の良い改善は決して不可能ではございません。それを可能にする手札を我々はこれまでの経験やノウハウ、さらに数多の協力企業様の力も借りて揃えることができます。もしお困りのことがございましたら、どんな無理難題でも一度ご相談くださいませ。皆様のより良い装置作りの一助になれると自負しております。
今回も最後までお読みくださりまして、ありがとうございました!