投稿日:2021年5月10日
私たちOEM装置設計・製造comではその名の通り、医療機器や食品機械などの装置を材料発注から機械加工・組立して納期までに完成品の納品まで…と、一貫して対応するOEM受託製造を行っております。
今回はいつものようなお取引メーカー様での事例ではなく、このページの運営会社「ZESTIA」の事例になります。実はZESTIAは自社商品「YURUSOR」という商品を展開している、“緩み監視センサー”のメーカーでもあります。今回はそのYURUSORのブラッシュアップ時に実際に発生したVE事例のご紹介です。
加工方法の見直しで50%もの大幅コストダウンにつながった事例になります。
1.はじめに
YURUSORとは?
OEM装置設計・製造.comを運営しているZESTIAの自社商品で、貨物の運送時に荷台のラッシングベルトやレバーブロック(チェーン)に取り付け、運行中に緩みが発生した際に即座に運転席にお知らせする「固縛の緩み監視センサー」です。弊社が手掛けるOEM装置を納品の為に輸送する際、トラック庫内でラッシングベルトが緩んでしまい、運送中の装置にキズが付く事例が発生したことをきっかけに開発した商品になります(皆様の装置を輸送される際にも事故を未然に防ぐのに貢献できると思います)。
目的を輸送・運搬の安全性向上としていることもあり、耐久性や軽量性・製品としてのコストパフォーマンスなど、随時改良していきたい要素は多々ありました。
今回はYURUSOR内部の一つの部品についてクローズアップしていきます。
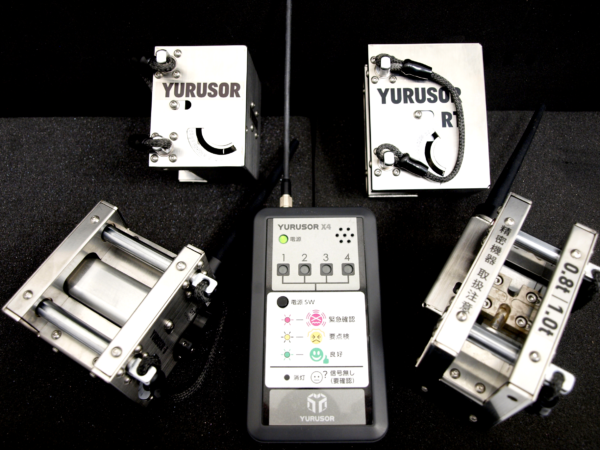
2.滑り金具のVE事例
この事例は、YURUSORの価格低減を目指した改良検討時に実行した、加工時間削減のためのVE案件になります。YURUSORという製品の使用環境は、荷物の運搬時に屋外で使われることもあり高い耐久性が求められます。そのため初期の設計時にはなるべく無駄は省きつつも安全率を優先して頑丈に、かつ重くなりすぎないようにアルミ材などを活用しながら構成部品を考えておりました。
今回一例として取り上げさせていただくのはシャフトが摺動する際のガイドとなる「滑り金具」になります。前述のように堅牢性と軽量性といった特徴を両立させるためにアルミの切削品(フライス加工)にブッシュを圧入した形になっております。
下の写真をご覧ください。
アルミ製滑り金具
3.求める機能と改善に向けた課題
弊社がこの部品に求める機能としては、
・繰り返し使用してもへたらない摺動性
・過酷な使用環境に適応できる耐久性
・都度の取付が面倒にならないような軽量性
ひとまずこの3点でした。ブッシュを圧入することで摺動性を、ブロック形状で板金ケースの変形を抑える耐久性を、材料をアルミにすることで軽量性を実現しておりました。求める機能を想定通りに満たしてはおりましたが、製品は常にアップデートを求められるものです。そこでより良い製品にするためお客様の声も含めた課題の洗い出しを行いました。
➢ブッシュの摺動性は良いが、圧入の手間と購入コストがかかる
➢板金の変形を防ぐ目的もありブロック形状にしているが、
1つ1つフライス加工するのに時間がかかる
➢アルミ製の為補助的な耐久性はあっても部品自体の強度が心許ない
会議の中で意見を出し合い上記のような課題が出てきました。
そこで課題解決のために試行錯誤し、形状変更を実施しました。
ステンレスで作成した滑り金具
4.VE内容とその効果
①材質をアルミ→焼入のできるステンレスへ変更(材質の強度向上・ブッシュの削減)
材質をステンレスへと変更したことで部品自体の強度が向上しました。それに伴いブッシュ(購入単価@600程)が不要になり、シャフトの摺動も問題なく行えます。また、以前はブロック形状で板金を補助していましたが、板金自体の強度を向上させるために計算して必要な厚みを持たせたり、形状変更を施すことで滑り金具にその補助機能が不要になりました
②形状を四角→丸へ変更(加工時間・工程の集約/低減)
形状の変更も行いました。以前はフライスで1つ1つ切削加工→ブッシュの圧入と2段階あった加工工程が複合旋盤1台で完結できるようになりました。また、1本の丸棒から連続で加工できるため着脱の手間も大幅に削減でき、ブッシュの圧入も削減できました。
③形状の変更により4か所全てへ同一部品の適用が可能に(図面数削減・共通部品化による単価低減)
以前の物は形状が2種類ありましたが新型の部品は1種類になり、4か所すべてに同じ部品を使用できます。図面枚数が減ることで加工準備時間の削減にもなります。一度に多く加工した方が材料や加工の観点からもコスト削減につながります。
上記3点が今回のVE内容と、その結果として得られた効果となります。
5.まとめ
今回はお客様ではなく社内で稼働している製品について、普段と比べれば幾分か自由に意見を出し合いVEへとつなげることができました。今回メインに据えていたのは「加工にかかる時間や工数・無駄なコストの低減」でした。もちろんVEですから「機能を落とさず」というのは前提にありますが、今回の取り組みによって部品自体の「価値」は確実に向上しております。部品自体の耐久性・強度の向上ももちろんですが、ブッシュで補っていた摺動性を部品の機能として集約できたこと(機能の向上)。また、部品ができるまでの時間や工数を大幅に削減できたことで50%ものコストダウンにも成功しています。
我々は普段お客様の部品・装置に対するVE提案を行っておりますが、それは「第3者視点で見つめなおすことで見えてくることも多々ある」という視点からのご提案でもあります。皆様のリリースされている製品や装置を一番良く知っているのは、もちろん開発・販売等をされている皆様です。今一度、部品や装置のコストパフォーマンスを見直し、製品が持つ価値を最大限引き出すためにはどうしたらよいか…検討されてはいかがでしょうか?
皆様がこれまで蓄積された知恵やノウハウ、技術力を応用することでコストダウンは十分可能です!
とはいえ初めて取り組まれる際はノウハウの蓄積が薄い分野などがあると思うように改善が進まないこともあるかと思います。その際にはぜひこの「OEM装置設計・製造.com」に掲載されております事例集をお役立てください。部品加工や装置の事例集も随時更新しております。
最後までお読みいただき、ありがとうございました!