投稿日:2024年10月7日
OEM装置設計・製造.comを運営するZESTIAは、装置設計から対応しています。装置設計における要素検討は、装置や個々の装置部品が設計通りに機能するか分析するプロセスです。また、強度試験や耐久性試験などを通じて、設計段階での問題点を早期に発見し、製品の信頼性を高めることも役割の一つです。
食品機械メーカーのお客様からトレイシール機の開発依頼をいただきました。当初は部分的な設計変更のご依頼でしたが、装置重量が2.9tと重く、コストが1600万円と高額である点から、全面設計変更になりました。
当社では、装置重量の軽減と製造コストの低減を目指し、以下の要素検討を行ないました。
⑴装置部品の材質変更
食品機械のため、ステンレスを多数使用していましたが、衛生上問題のない箇所にまでステンレスを用いていたため、食品に接触しない箇所は、鉄に対してメッキ処理または塗装を施した部品に変更しました。また従来の設計では、スクラップ巻き取り箇所もオールステンレスでしたが、これをアルミに変更することで、重量の軽減と材料コストの削減につながりました。
⑵装置構造の変更
強度計算により、架台に必要な強度を算出した結果、チェーン駆動からベルト駆動に変更できることが判明しました。これにより、部品点数が約200点削減でき、装置全体の重量を低減することができました。また、コンベアの下部に配置される電装ボックスに必要な強度も下げられたため、フレーム構造からモノコック構造に変更することで、更なる重量低減につながりました。
さらに、トレイシール機で必要な真空状態を維持するために、1枚のアルミプレートに深穴加工で流路を設けていましたが、専用工具の準備と加工時間を考慮し、パイプとマニホールドに置き換えることで、従来の機能を維持したまま、装置の製造コストを削減することができました。
上記以外にも、既存設計から変更することで、装置の重量および製造コストを削減できる要素を洗い出しました。それぞれの要素を試験することで、最適な装置構造を導き出し、本設計を開始しました。
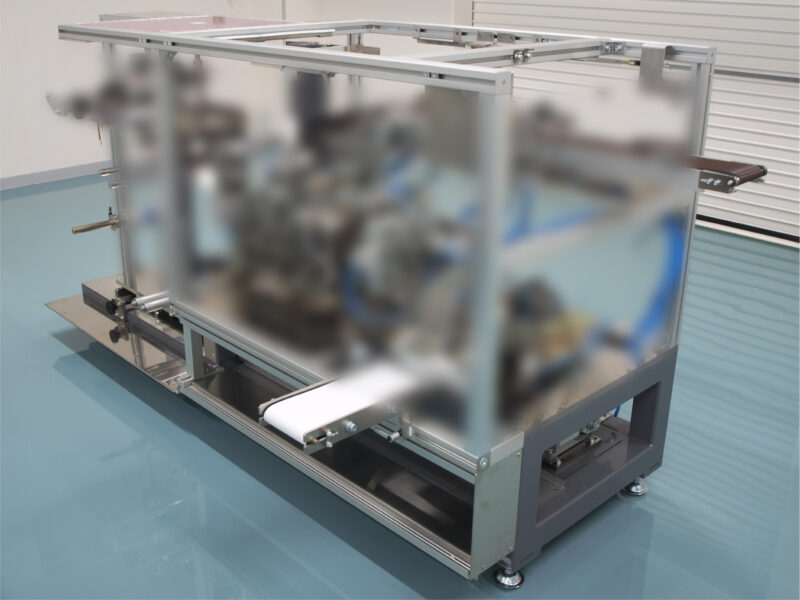
再設計された本機は、従来より装置の重量が1/10、製造コストが約40%削減され、1000万円で装置開発が出来るようになりました。具体的な設計変更内容は以下の通りです。
①装置部品の材質をステンレス+アルミからステンレス+アルミ+鉄に変更
②チェーン駆動式をベルト駆動に変更
③電装ボックスの構造をフレーム構造からモノコック構造に変更
④真空流路をアルミプレートからパイプ+マニホールドに変更
⑤配線と配管の位置調整によるメインフレームの構造変更
⑥安全カバーをマシンシャッターからフレーム+板に変更
⑦使用するパイプ径を1つに統一
OEM装置設計・製造.comを運営するZESTIAは、装置設計における構想設計、要素検討・試験、基本設計、詳細設計の全てを自社で完結しています。装置を構成する各種部品や構造が装置の機能に直結するという誤認識から、過度な設計になっている場合があります。そのため、こうした要素を取り出して検討することでコスト削減につながります。装置開発をご検討の際は、ぜひお気軽にご相談ください。