投稿日:2024年1月11日
装置を設計する際には、構想設計の段階で各部品ごとに強度計算を行う必要があります。なぜなら、装置の部品が配置される場所で掛かる荷重が異なるため、必要以上の強度を持たなければ、部品交換頻度が高まってしまうからです。最悪の場合、装置の再設計が必要となりますので、実機を製造する前に数値的に検証することを推奨します。
お客様から装置の製造原価を見直したいという依頼いただきました。構造を確認した結果、電装ボックスが過剰設計されていることが判明しました。具体的には、食品製造ラインで使用されるため、異物混入の防止を重視してステンレス鋼板が採用されていました。加えて、電装ボックスの上部に部品が配置されることから、変形を抑制するためにステンレス鋼板を全周溶接したモノコック構造を採用されていました。
しかし、電装ボックスの上部に配置される部品は、バランスよく配置されるのではなく、荷重が集中する箇所とそうでない箇所が存在します。そのため、モノコック構造は過剰な設計となり、装置の重量を余分に増加させる要因となります。製造原価と装置重量は密接な関係にあり、設計段階から電装ボックスのどの部分にどのくらいの荷重がかかるかをシミュレーションして、最適な強度を導き出す強度計算が必要であると当社は考え、提案いたしました。
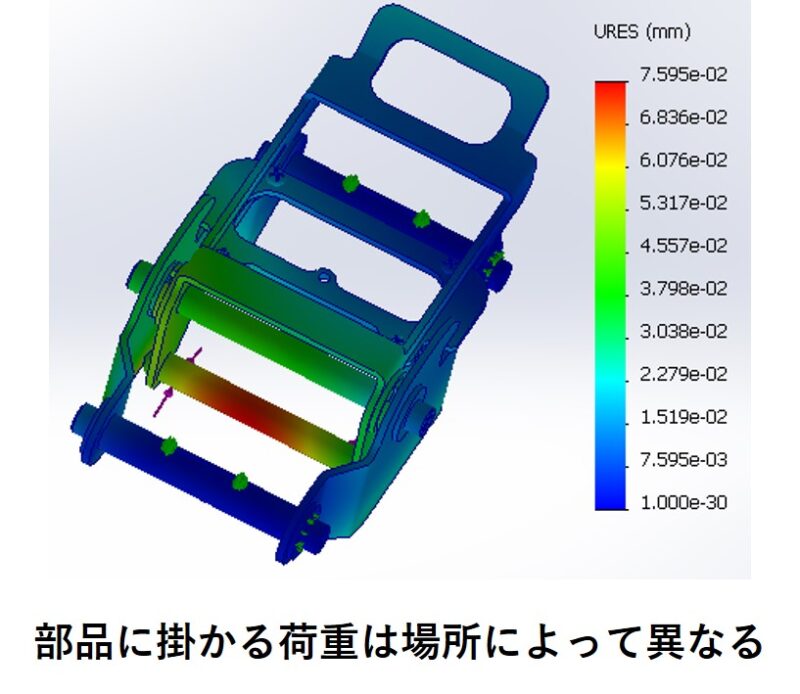
そこで、当社はまず3D CADシミュレーションによる強度計算を行い、各部品ごとに掛かる荷重を明確化しました。そして、強度が要求されない部分については、ステンレス鋼板からアルミフレームに変更し、点付溶接とシリコンを用いて電装ボックスを製作しました。この設計変更提案によって、装置重量は1/2に軽減し、製造原価も1/4までコストダウンに成功しました。

OEM装置設計製造.comを運営するZESTIAは、装置設計から製造、組立まで一貫対応しており、装置製造前には必ず強度計算を行うことで、お客様の装置の製造原価低減や長寿命化を実現してきました。さらに、食品機械、半導体装置、搬送装置など、各業界ごとに採用されている構造を熟知し、これを次のお客様の装置製造に生かすことも強みの一つです。装置の再設計や量産装置のコストダウンをご検討の方は、どうぞお気軽にご相談ください。