投稿日:2020年11月12日
「OEM装置設計・製造.com」を運営するZESTIAでは、医療機器や食品機械などの装置を、材料発注から機械加工・組立、そして納品するまで一貫して対応するOEM受託組立製造を行っております。今回は、装置単体ではなく将来的な展開の仕方まで考慮したVE提案を行った事例をご紹介いたします。
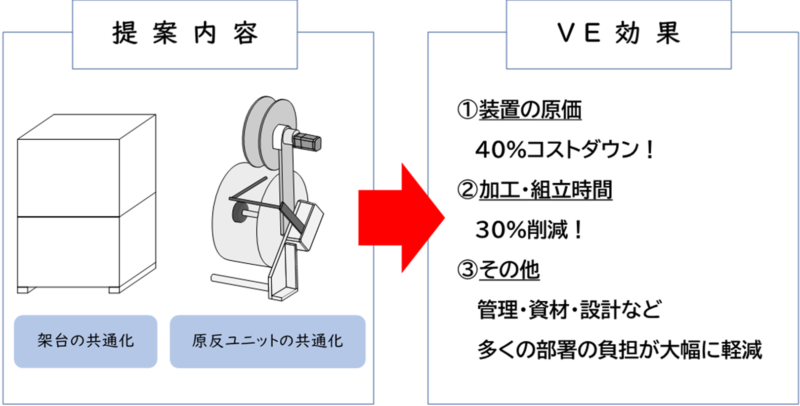
今回ご紹介するのは、機械・装置を複数のシリーズ展開されているメーカー様に対して「パーツや架台の共通化」を提案させていただき、手間やコストを徹底的に省いた結果、「原価で40%ものコストを削減」できた事例です。
一口に機械・装置と言っても、スペックや用途、お客様に合わせた特別仕様など、同じ機械でもリーズナブルなエントリーモデルからスタンダード機・ハイスペック機など用途に合わせたいくつかの「仕様」に分かれている事があります。また、同じ目的でもターゲット層やバージョン違いで様々なシリーズをラインナップされているメーカー様も多いかと思われます。そんな中、市場やお客様のニーズに合わせて日々開発・設計をされているメーカー様の苦労や苦悩は想像を絶するものと思われます。
毎回設計の方に求められるのはニーズに沿った設計・その都度お客様に合わせた設計変更など、時間の限られた中で機械・装置を形にしていくものでしょう。それはとても大変なことですが、必要なことです。市場やお客様に合わせて変化できるメーカー様は日々絶え間ない努力をされており、一様ではなく各々の企業様の努力は並々ならぬ事と思います。
--------装置メーカー A社様の事例--------
今回紹介させていただく事例も、弊社のお付き合いさせていただいているメーカー様でのお話です。そのメーカー様も、様々なタイプの装置を設計・製造し、販売されております。ニーズの変化に対応し、新機種を度々発表されておりました。そして海外進出を考えていたメーカー様は、進出先の中国のメーカーの類似機種のスペックの高さもさることながら、価格の安さに驚き、弊社にご相談いただいたというのが経緯です。
弊社ではこれまで同様図面を1枚1枚見直し、材料や加工方法など見直してコストダウンをしようとしておりましたが、その機械は量産前にすでにVE提案をさせて頂いており、そこからさらに価格を下げるのは、従来の方法だけでは難しい状況でした。しかしスペックは同等まで向上させ、価格も抑えなければ同じ土俵に立って参入することは叶いません。
そこで次のような提案をさせて頂きました。
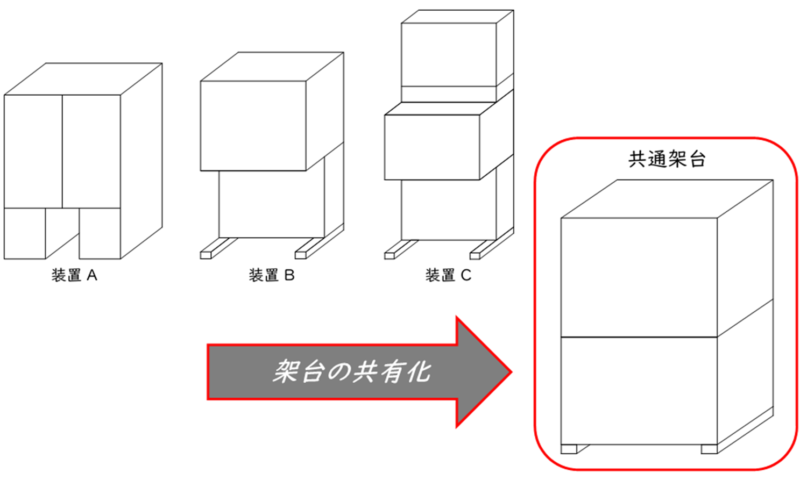
---------- 現状での 問題点 ----------
上の図を見て頂くと、概要図ではございますが仕様の違いに起因する形状の差異が見て取れるかと思います。その時々でベストの状態に作り上げることで、様々な差異が装置ごとにあるため、仕方のないことですがその都度加工や組立にかかる時間は増えてしまいます。
それは仕様が違うため、以前製作した類似品があったとしてもデータづくりや毎回の需要に合わせた細かな変更点などにより、加工時のデータづくりや組立方法のすり合わせなど、これまでに積み重ねた類似の装置作りの経験をそのまま活かせず、都度図面や実物に対して応用していく必要があるためです。
例えば加工の場合ですと、前述の通りデータ作りです。ほぼ同じ図面で数か所の穴位置変更などであればデータを流用して変更を加えることは容易ですが、多くの場合新規図面になることが多く、そのたびに加工者はデータを1から作成する必要に迫られます。組立に関しては、類似の装置を作った経験があるからこそ、変更点を設計者と詳細に打合せ、注意して作業に当たらないとなまじ似ているため間違えてしまう危険性があります。組立従事者もそれは重々承知の上ですので、作業工程を通して確認作業が多くなり、新規案件に取り掛かる場合と同程度の作業時間がかかってしまいます。
実際の物づくりに関してこの2点だけをとっても、何か対策を講じることで作業時間の短縮が可能なのではないかと考えました。
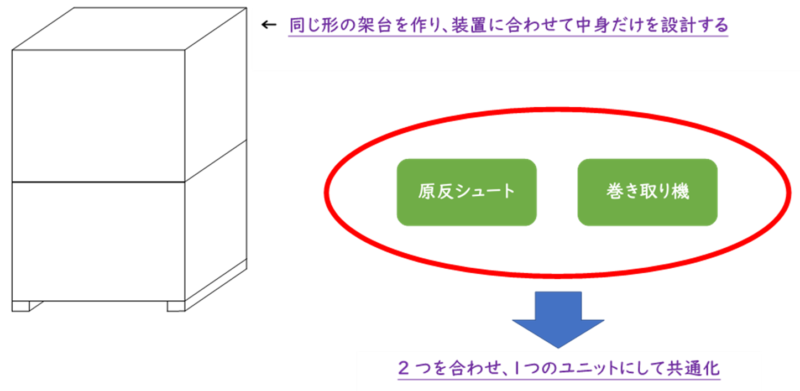
-------- V E 提案内容と その効果 --------
仕様の違う装置でも、統一できるパーツはないかと考えた我々は、架台や原反を複数機に適応できるような設計変更の提案を行いました。具体的には原反を5機種で共有、架台を3機種で共有することができました。
これにより、加工するためにデータを新しく作成する手間が削減でき、加工を完了するまでにかかる時間が大きなもので「1時間/1図面」削減できました(1部品あたり)。そのため全体を通して部品加工にかかる時間が大幅に削減でき、納期の短縮にもつながりました。そして組立に関してもメリットがあります。同じ架台やパーツを適用することで、複数の装置で同じ内容の組立部分が発生します。装置ごとに綿密な打ち合わせを行ったり、注意事項を把握するためにやり取りをする時間が削減できます。
また、設計者にとってもこれまでは新しい装置を構想する際に全て新規で設計をしていたため、架台の共通化をしたことで中身の非共通部分の検討に注力できます。また、手配履歴のある部品が増えることで新たに見積りを取ったり価格の比較・検討をしたりといった手間が削減できるため、管理や資材の方の負担軽減にもなります。
------------ まとめ ------------
結果として装置全体で元の原価を100%とした時、提案後は60%にまで削減することができました。もちろんコスト削減のみならず、設計完了が早くなり、手配の手間が減り、加工がすぐ始められ、組立も効率が上がる…と様々な部署で高効率化を実現し、各担当者の負担軽減、納期の大幅な削減にもつながりました。
いかがでしたでしょうか?今回はメーカー様では「あるある」かもしれませんが、装置のバリエーションが増えることによる負担の軽減・高効率化を含んだVE提案となりました。「装置の架台を統一してしまえばあとは中身を変えるだけ!」…と言うのは簡単ですが、今ある装置をそれぞれ適応させるには綿密な打ち合わせをして、思案・検討を繰り返しました。これまでの単体でのVE提案とも違い、弊社としても規模の大きなご提案となりましたが、その分製作を完了したときのお客様と分かち合う達成感や、40%ダウンできたという結果は期待を十二分に上回るものとなりました。
世の中には様々な装置が存在します。皆様の装置は、「現状」がベストでしょうか?
大変ではありますが、得られるものは決して小さくないと思います。ぜひ皆様も、装置がより良くあるための検討をしてみてください。つまずくことがあれば、ぜひこのサイト、「OEM装置 設計・製造.com」をご活用ください!
ZESTIAでは、加工・組立の部署のみならず、営業・管理・資材・梱包・検査…と、社内の全部署がコストダウンに関わる取り組みを行い、お客様にご提案をさせて頂いております。お困りのことがございましたらお気軽にご相談ください!
最後まで読んでいただき、いつもありがとうございます!